Hi Yuneec Pilots,
my name is Wolfgang, I'm from Austria and I just started to fly a Typhoon H.
Unfortunately after some flights, the drone crashed and the cgo3+ got damaged.
Í hope you guys can help me with that.
The obvious damages on the CGO3+ were:
-) A crack in the upper plastic part of the camera casing (which should not be a problem now)
-) The front plastic cover was off and the 5Ghz-antenna smiled at me (I put the cover back on)
-) The camera ball with the arm around it has disconnected from the vertical arm (the 3 screws which connect onto the roll motor)
So I dismantled the camera, to get access to the screw-holes of the roll motor.
Then I screwed in 1 screw, which I have found again, so that the roll motor is connected again. -> see picture
Then for testing reassembling all parts and make a test.
I have uploaded a video about the start-up of the cgo3+ and the behaviour of it.
we.tl
What I have found:
-) The Wifi-connection to the ST16 is OK and I have a video link
-) The error beep codes looks like it means that there is a problem on the tilt encoder (which would be the one directly on the side of the camera ball where it is mounted)
-) It looks like that the movements of all motors are OK, but in the end position (home position) it is not able to get a good lock in position
Is it possible, that during the disassembling of the camera (to get to the roll motor screws), that I have turned the tilt motor and so the position is now not correct anymore?
I have read some articles about it, where it states that this can be a problem.
Also I need some spare screws for the roll motor to screw in all 3 screws and not just one. Does anybody know the dimension of these screws?
I hope you guys can help me.
Thanks in advance
Wolfgang
my name is Wolfgang, I'm from Austria and I just started to fly a Typhoon H.
Unfortunately after some flights, the drone crashed and the cgo3+ got damaged.
Í hope you guys can help me with that.
The obvious damages on the CGO3+ were:
-) A crack in the upper plastic part of the camera casing (which should not be a problem now)
-) The front plastic cover was off and the 5Ghz-antenna smiled at me (I put the cover back on)
-) The camera ball with the arm around it has disconnected from the vertical arm (the 3 screws which connect onto the roll motor)
So I dismantled the camera, to get access to the screw-holes of the roll motor.
Then I screwed in 1 screw, which I have found again, so that the roll motor is connected again. -> see picture
Then for testing reassembling all parts and make a test.
I have uploaded a video about the start-up of the cgo3+ and the behaviour of it.
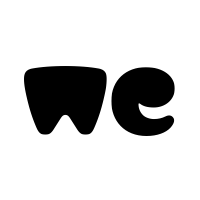
20211026_174708.mp4
1 file sent via WeTransfer, the simplest way to send your files around the world
What I have found:
-) The Wifi-connection to the ST16 is OK and I have a video link
-) The error beep codes looks like it means that there is a problem on the tilt encoder (which would be the one directly on the side of the camera ball where it is mounted)
-) It looks like that the movements of all motors are OK, but in the end position (home position) it is not able to get a good lock in position
Is it possible, that during the disassembling of the camera (to get to the roll motor screws), that I have turned the tilt motor and so the position is now not correct anymore?
I have read some articles about it, where it states that this can be a problem.
Also I need some spare screws for the roll motor to screw in all 3 screws and not just one. Does anybody know the dimension of these screws?
I hope you guys can help me.
Thanks in advance
Wolfgang